Blog, Vlog, Whatever… Ravings of a Tone Madman.
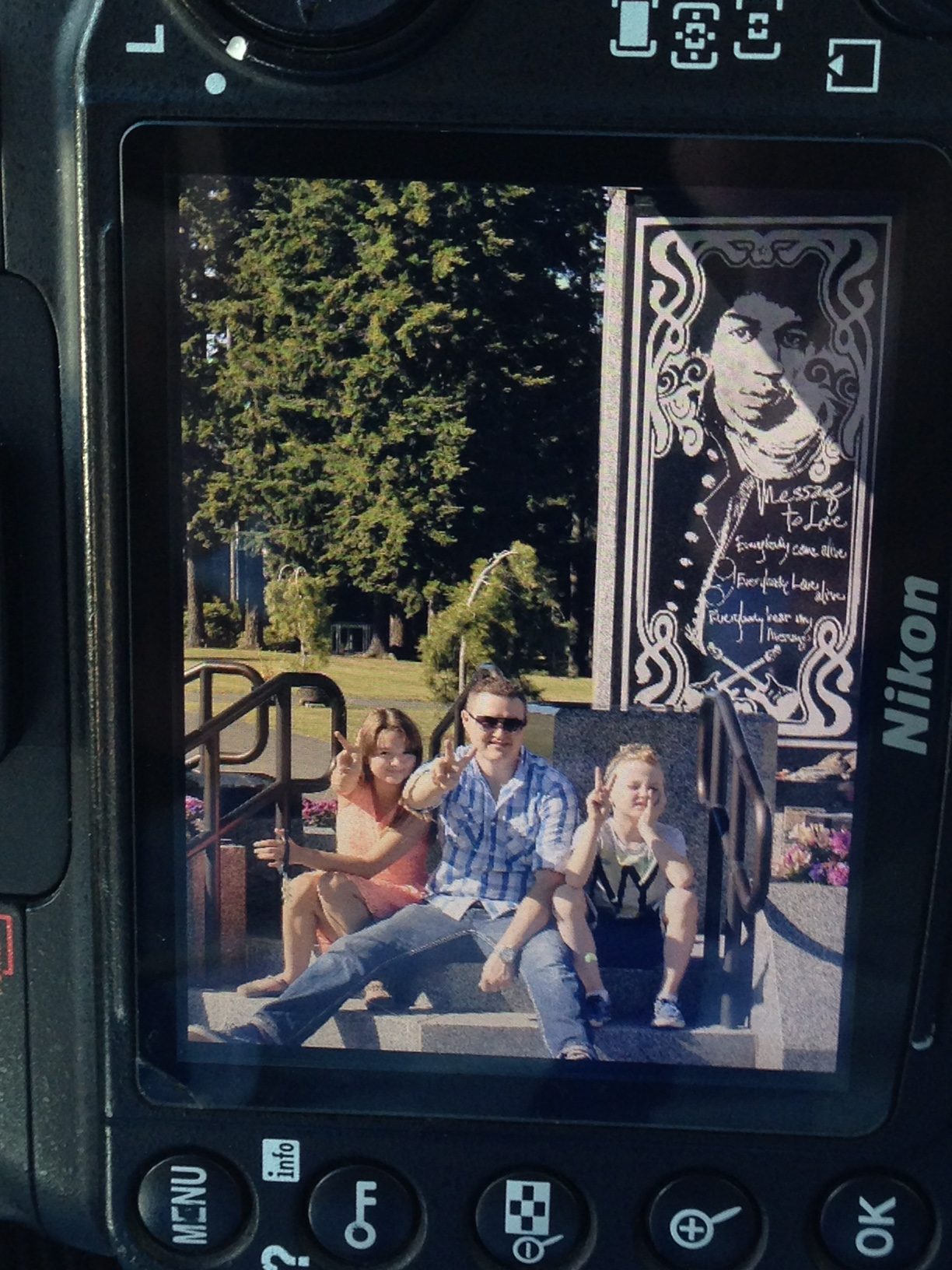
Dec 4 2020
What a year? As I approach this holiday season I’ve got a lot to be thankful for. I was browsing through my camera roll on my phone and came across a picture I hadn’t looked at in quite a few years. My kids are much older, teenagers in fact, now so this had to have been at least 7+ years ago. Anyhow, back to my point ( I eventually get there). I’m unfathomably thankful for my family. My wife is the best, a true partner. She took this picture when we were visiting the grave of Jimi Hendrix on a side trip from one of her photo shoots in Seattle. It is because of her hard work and determination in her work that I am getting the chance to now take my passion for music and guitars and turn it into something I can share with the world. There will be a lot of ranting to come, but I wanted to start this endevor with gratitude.
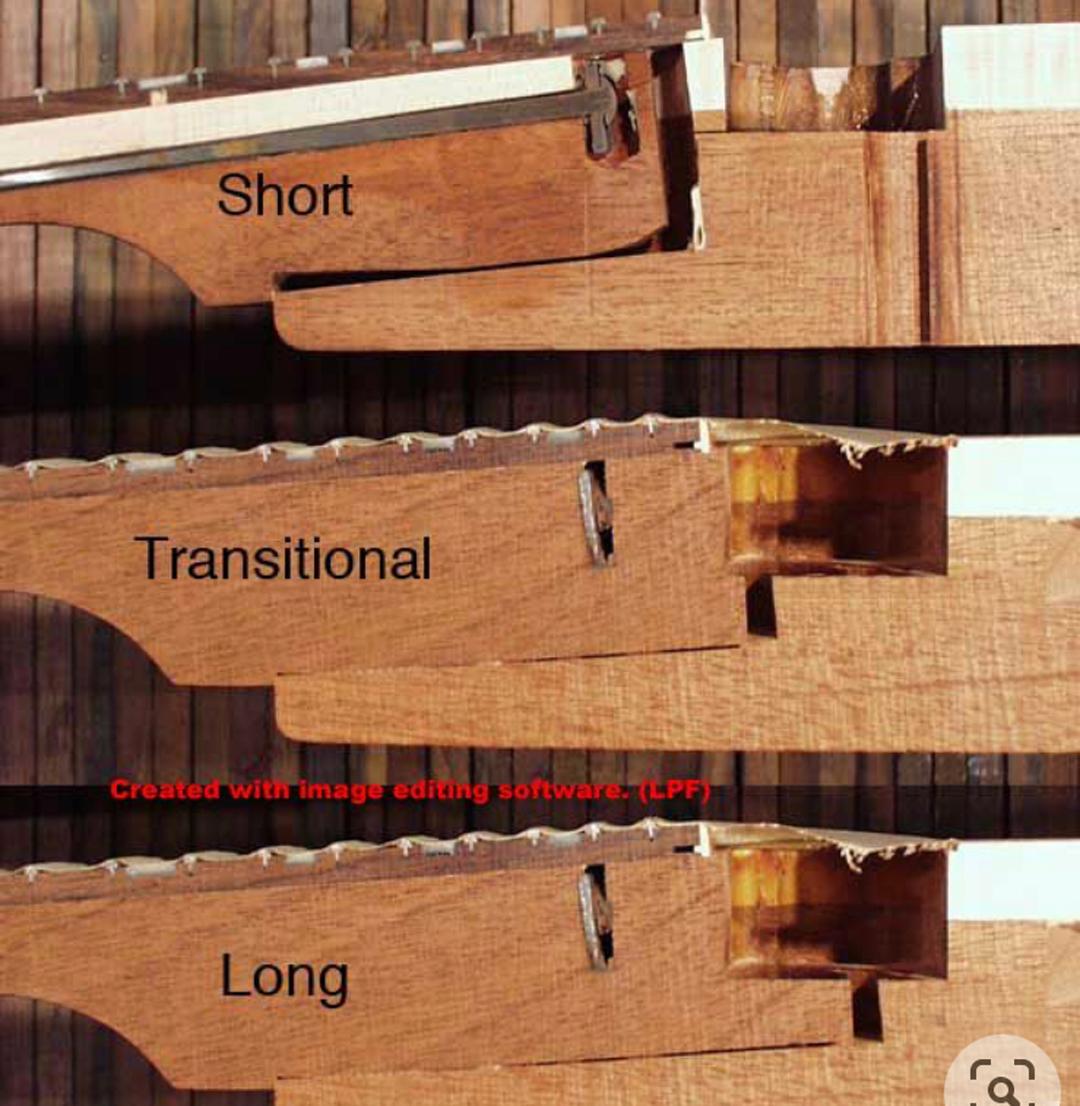
Neck Tennon, December 13, 2020
I’m going to vent a bit about neck tenon length. While there is something to be said for size, length, girth, relative mass etc, I think HOW you use it is probably more important. The image in the bio is supposed to be of 3 different Gibson Les Paul Standards, one from each era, 60’s 90’s and modern. Now given that I’ve seen this picture floating around the internet for at least 10 years, I can not verify its authenticity. I’ve never cut a gibson ( or any other guitar for that matter) in half just to look at the construction. I have done my share of neck repairs and seen pictures of smashed guitars (rock on!) that show the interior construction pretty well.
Back to the image. Where this image has shown up in forum posts and other discussions, the topic is always about tone and the length of the neck tenon. The thinking is the longer the tenon, the better tone. I have a different opinion. While there needs to be a minimum amount of surface area contact between the body and neck, the key to achieving a clear and lively tone is more likely in the construction of the neck pocket and the mating of the neck. In the top image, supposedly of the modern Gibson non custom shop build, you can see that the bottom of the neck joint is slightly rounded to assist in mass production of getting the neck break angle just right. This sacrifice to expediency, in my opinion, diminishes the liveliness of the instrument by reducing surface area contact that is not stuffed with filler, glue etc. The middle image is supposed to represent the 90’’s golden era of “good wood” gibsons. The thing that stands out to me is that the neck pocket and joint are built like a puzzle piece, they fit. More contact equals better tone. The bottom image represents the long neck tenon of the 60’s era “Holy Grail” Gibsons. While it does have a small amount of extra mass, the picture clearly shows a better neck to pocket fit.
I’ve personally experimented on this with a few early builds and what I found is that while there are subtle tonal differences, they are more likely due to the characteristics of the wood used. I suppose one could build two identical guitars from the same cuts of lumber from a single tree if you really wanted to control the variables. My design of the SP and DP series utilizes a tenon that extends to be back of the neck pickup cavity. This extra long tenon requires a little more work but allows me to create more surface area contact, IF the pocket is cut correctly. Building ONE neck for ONE guitar allows for perfect fitment. The passable standard for me is build the neck slightly too tight, then sand back until only about .05-.12 MM of gap exists on any contact point. I picked up on this by watching Brian Monty build a 59 replica and use a sheet of copy paper to check his pocket. ( https://www.montyguitars.com/about )
So back to the old adage about the ship, It’s not the size of the ship but the motion of the ocean.

12/18/20 More on Neck Tennon - Angled Neck Pocket
A topic that comes up commonly among builders of solid body carve tops revolves around the process of cutting the neck pocket. I’ll refer to these exaggerated graphic examples to illustrate my thinking on the subject. These drawings are rudimentary and not to scale, but should suffice for discussion sake. The traditional method requires that a jig is used to set the angle of the router as the neck pocket is cut (see top graphic). The other method that is common among newer builders with fewer tools is to cut the neck pocket square, and use a saw to set the angle in the neck tenon (bottom graphic). As you can see both methods leave you with the same resulting neck break angle. So….does it matter? Let’s look more closely. The top drawing shows more mass left in the body at the back of the pocket and less near the joint. Depending on the overall thickness of the body, this could create a weak joint (think of all the early Gibson SG’s that broke at the body/neck joint. I believe this was a result of the traditional tooling taking too much mass out of the most critical strength area. You don’t see many PRS or Les Pauls breaking here. This is largely due to the increased mass at the joint due to the body thickness in my opinion. So from a strength/durability the square/flat neck joint is probably a safer bet, so why hassle with the jig at all? Opinions vary but most say that by aligning the jig to the angle of the body carve (carve tops typically have the portion of the body where the neck meets the body carved to make a more graceful transition), thereby ensuring that everything flows at the same angle. I like the simplicity of this because it ensures a tight fretboard to body fit. Have you ever seen guitars where the back of the fretboard rises off the body?
So this is a tone blog and what does any of this have to do with tone. In my opinion both methods can be done right or wrong, each either adding to poor tone, or good tone. In both examples, if the neck is not fit perfectly, the resulting gap created will reduce resonance, decouple the vibration of the string from the body, and may introduce a twangy tone. If care is taken to measure all the angles to ensure a tight fit both in the pocket and at the butt joint (rear vertical surface of neck) then either work and on thinner body guitars, the square pocket method may even be superior.